
Differences Between Collaborative Robots and Industrial Robots
In modern manufacturing, robotic arms play an increasingly vital role. However, depending on the application and requirements, the type of robotic arm can differ significantly. This article explores the five key differences between collaborative robots (cobots) and industrial robots, helping businesses make informed decisions when choosing automation solutions.
🤖 Definition and Purpose
Collaborative Robots (Cobots):
Collaborative robots are designed to work alongside human operators to enhance work efficiency and quality. These robots aim to reduce repetitive tasks, ease the burden on human workers, and ensure safety throughout the operation process. Cobots are particularly beneficial for tasks requiring direct interaction with humans, such as assembly, logistics, and inspection.
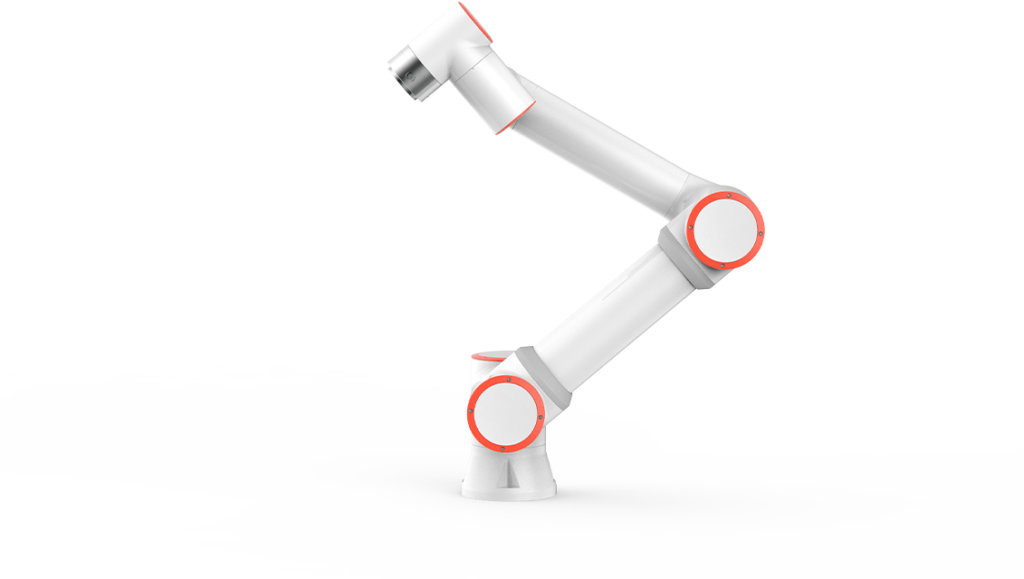
Industrial Robots:
Industrial robots are primarily designed for fully automated production lines, enabling high efficiency, precision, and consistent production. These robots specialize in repetitive tasks such as material handling, welding, painting, and assembly, significantly boosting productivity in large-scale manufacturing environments.
🔧 Design and Structure
Collaborative Robots:
- Lightweight Design: Cobots are often made with lightweight materials to reduce inertia and energy consumption, making them easier to deploy and move across workstations.
- Flexible Joint Design: Cobots feature highly adaptable joints, enabling them to operate efficiently in complex workspaces and handle tasks requiring different levels of precision.
- Built-in Safety Features: Cobots are equipped with advanced sensors and safety systems, such as collision detection, force and speed control, and emergency stop functions, ensuring worker safety during operations.
Industrial Robots:
- Rigid Design: Industrial robots are built with more durable and rigid materials to ensure stability and longevity, even in demanding industrial environments.
- High-Precision Joint Design: Industrial robots have joints designed for extreme accuracy, ensuring precise control over position, orientation, and movement.
- High Payload Capacity: Industrial robots are capable of handling heavy-duty tasks with larger payloads, making them ideal for lifting heavy objects and performing extended operations.
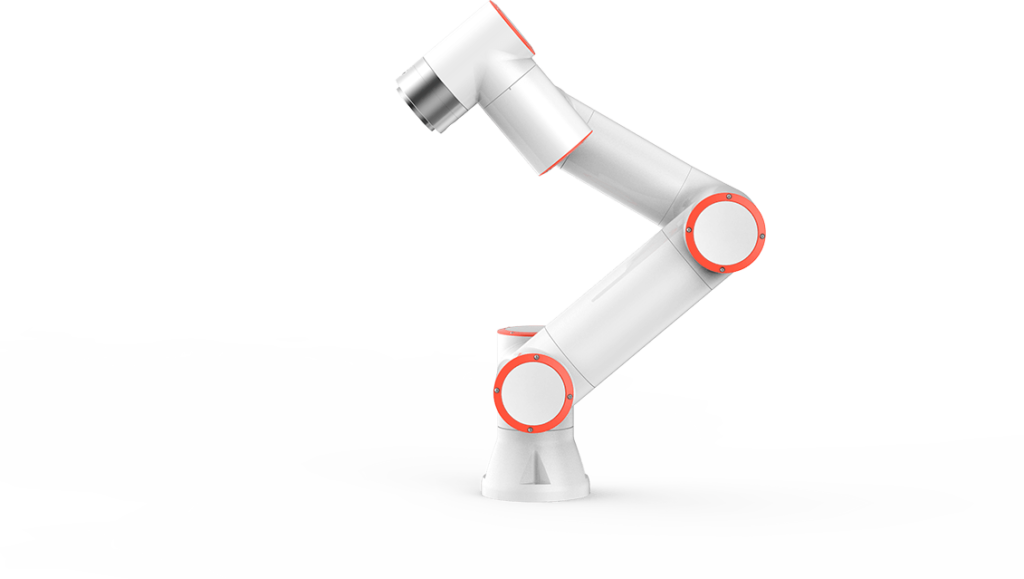
🏭 Application Scenarios and Work Modes
Collaborative Robots:
- Ideal for Close Human Interaction: Cobots are well-suited for tasks requiring collaboration with humans, such as assembly, logistics sorting, and simple quality inspections. They excel in small-batch production and dynamic environments where flexibility is key.
- Work Modes: Common tasks include pick-and-place, lightweight assembly, inspection, and machine tending.
Industrial Robots:
- Perfect for Large-Scale Automation: Industrial robots are used in continuous, high-volume production lines, such as automotive manufacturing, electronic product assembly, and heavy industries.
- Work Modes: Tasks often include material handling, complex welding, high-precision painting, and machining, often requiring integration into rigid, pre-programmed workflows.
📊 Key Differences at a Glance
- Interaction with Humans: Cobots are designed for direct human interaction with built-in safety features, while industrial robots typically operate independently, often isolated for safety reasons.
- Deployment Complexity: Cobots are easy to program and deploy, suitable for dynamic environments, while industrial robots require more complex programming and setup.
- Flexibility vs. Efficiency: Cobots prioritize adaptability and flexibility, while industrial robots focus on speed and efficiency for repetitive tasks.
- Payload Capacity: Industrial robots handle heavier loads and high-speed operations, whereas cobots are limited to lighter, less strenuous tasks.
- Safety Features: Cobots are equipped with extensive safety mechanisms, making them safe to work alongside humans, unlike industrial robots, which require physical barriers for safety compliance.
🔍 Benefits of Collaborative Robots in Warehousing and Steel Welding
Cobots are increasingly popular in warehousing for material handling and sorting, as well as in steel welding, where precision and safety are essential. For example, portable welding robots and handling automation robots are used in diverse environments to optimize workflows. These cobot collaborative robots enhance both productivity and worker safety while reducing operational costs.
Industrial robots, on the other hand, dominate heavy-duty tasks and large-scale production environments. From big weld robots for automotive manufacturing to handling automation robot workstations, their contribution to modern factories is indispensable.
📈 Conclusion and Future Trends
Both collaborative robots and industrial robots play critical roles in the evolution of manufacturing and automation. While cobots focus on enhancing human-robot collaboration with safety and adaptability, industrial robots are designed for high-speed, high-volume tasks.
With advancements in robotics technology, the future promises smarter, more adaptive, and safer robotic solutions. Whether you’re looking for handling automation robots providers or portable welding robots, understanding these differences ensures the right choice for your specific needs. The collaboration between cobots and industrial robots will continue to drive the growth of intelligent, automated manufacturing systems.